Hydroforming
Hydroforming means the forming of parts by use of fluids as force transducers, compared to mechanical forces exerted by conventional presses. In niche industry sectors, the medium can also be gas or plastic pellets, which is no hindrance to process simulation with PAM-STAMP. Either tubes or profiles with closed cross-section are formed with inner pressure or flat blanks with one-sided pressure exertion, known as the Fluidcell process, or passive resistance against a mechanical forming, the so-called Aquadraw process.
During hydroforming processes of parts with closed cross-section, one would typically use axial punches to seal the part ends and push the material into the forming die, to achieve a higher expansion in areas near the part ends. Parts with branching such as t-pieces also need a counter punch to control the material flow into the branching. The possibilities inside PAM-STAMP fully cover all those technical aspects.
PAM-STAMP spans the entire virtual manufacturing chain of processes from tube bending and crash-forming or press bending over an optional consideration of annealing for stainless materials to the actual hydroforming, then trimming and optional end or further mechanical forming.
Typical customer challenges in hydroforming are similar to conventional sheet metal forming, with some additions. Starting from the final part, the hydroforming part design module PAM-TUBEMAKER supports the customer in reverse engineering workflow unto the required initial tube with all related manufacturing steps needed to achieve the final part. In reverse evolution, that means to cover the following challenges faced by the customer:
Determination of cross-section of tube or profile part
Design of bending line, with choice of a number of bends and bending radii (typically one radius), which can be adapted to available equipment to optimize production cost
Decide on an optional preforming operation
Estimation of landing zone i.e., cylindrical part of the tube end
Hydroforming die preparation
Initial tube dimensions
After an initial simulation run from the tube to hydroformed part, or partial run, in case of problems, the client can decide to optimize in a second or further loop and implement it within PAM-TUBEMAKER, adapting tools and processes to improve results. Simulation results answer all questions with regard to feasibility and necessary equipment on the shop floor:
Occurrence of local thinning, cracks or wrinkles
Need for specific lubrication, or possibly cam operation
Deviation of achieved form from CAD and also spring back of part
Required maximum pressure and related to that, closing force i.e. press size
Max. pressure and investigated axial feed/force determine the size of axial hydraulic cylinders
PAM-STAMP enables the customer to test and optimize the whole Hydroforming production theatre in one environment, while leaving the choice to use PAM-TUBEMAKER as starting point, or using available CAD data for all tools and parts to the customer. At the end of the day, all necessary data and information to deliver a reliable offer and feasibility statement are readily available
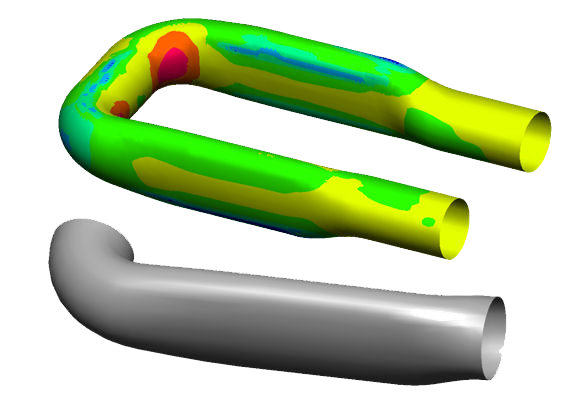